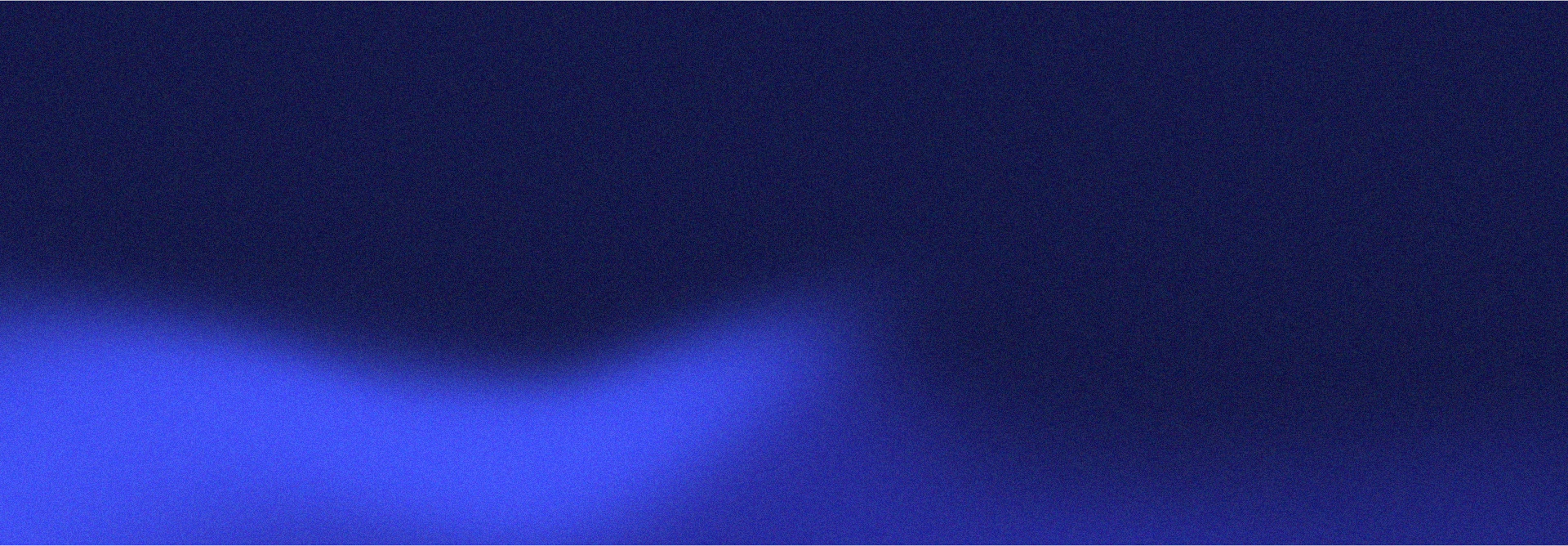
Coller FAIRR Protein Producer Index
About the Index
What is the Protein Producer Index?
This is the seventh edition of the Coller FAIRR Protein Producer Index, which assesses 60 of the largest, listed global meat, dairy and aquaculture companies on 10 material themes aligned with the Sustainable Development Goals (SDGs). The Index is designed to provide financial institutions with best-in-class data, analytics and trends on the protein sector to integrate into their investment decisions and engagement strategies.
The 60 Index constituents have a combined revenue of over US $518 billion in 2024. The companies were identified using the Bloomberg Industry Classification System and were selected due to their market capitalisation and material exposure to the five main animal protein categories (i.e., Beef, Dairy, Pork, Poultry & Eggs and Aquaculture). Companies assessed in the Index might be replaced if their core revenue-generating activities shift from animal protein production, if they are delisted or if other companies become more prominent in the sector.

Why are these risk and opportunity factors material for the animal farming sector?
We have worked with investors, companies and industry experts to create a methodology for evaluating 10 risk and opportunity factors.

How do we engage with companies?
We interact with companies at multiple stages of the Index production. After consulting with subject-matter experts, we ask companies for feedback on the proposed methodology. Once we have assessed them against the methodology, companies have a chance to review their assessment. Finally, once we launch the Index, we offer companies the opportunity to discuss their performance.

Which 60 animal protein producers are included?
Why have we selected companies that supply the biggest global food retailers?
Companies featured in the Coller FAIRR Protein Producer Index are key suppliers to some of the biggest global food retailers. These consumer-facing companies depend on Index-listed companies for their meat, fish and dairy and are consequently exposed to a broad spectrum of sustainability risks.
Global food retailers will struggle to achieve many of their sustainability-related goals (such as emission reduction targets, deforestation-free supply chain commitments, sourcing of antibiotic-free meats) without engagement and certification of their suppliers.
Members can now leverage the Index data to understand potential gaps and opportunities within the supply chains of some of the largest consumer-facing companies, using the new Supply Chain Analysis feature.
Related Reports
Disclaimer
The Coller FAIRR Protein Producer Index (the “Index”) referred to herein is published by the Farm Animal Investment Risk & Return Initiative (the ‘FAIRR Initiative’) for general informational purposes only.
The Index and the report have been compiled based on information made publicly available by the companies referred to therein or from other public sources, which information has not been independently verified, and neither the FAIRR Initiative nor the Jeremy Coller Foundation takes any responsibility for any such information. Neither the FAIRR Initiative nor the Jeremy Coller Foundation (1) makes any representation or warranty regarding the accuracy, reliability or completeness of this report, the Index or any information or (2) assumes any obligation to correct, update or supplement this report, the Index or any information. There can be no assurance that the Index or related reports or information will continue to be available, and publication of the Index and related reports or information may cease at any time, with or without notice.
The information provided on the terms and subject to the conditions stated herein or applicable to users of any website or other medium through which it is made available. Neither this report nor the Index nor any other information contained herein (1) constitutes advice, an endorsement or a recommendation of any kind or (2) should be used as a basis for making any investment or any other decision. Without limiting the generality of the foregoing, neither this report nor the Index or any other information contained herein (1) constitutes legal, regulatory, financial, tax, investment or other professional advice of any kind or (2) is intended or may be interpreted as, an attempt to market or sell any financial instrument. Recipients of this report have to seek their independent advice and may not rely on the FAIRR Initiative or the Jeremy Coller Foundation for any purpose.
Communicating about the Coller FAIRR Protein Producer Index
References to the Coller FAIRR Protein Producer Index (the “Index”) should not imply any endorsement, partnership, or accolade from FAIRR regarding an organisation.
The ranking an organisation receives in the Coller FAIRR Protein Producer Index does not indicate that the company or its protein sources are sustainable.
When discussing the company's ranking and/or risk categorisation, please consider the following details:
Factor reference: any reference to a risk factor score or risk categorisation should be labelled accordingly and should be made alongside all ten of the factors included in the Index, as well as a link to the FAIRR website.
The FAIRR logo should not be published alongside these descriptions on websites, on any type of label or product packaging, or in any marketing used to promote a specific food product.